What is Flexographic Print On Corrugated?
FLEXOGRAPHY
Flexography is typically the most economical option for large quantity orders with a bold, straightforward design. This option is often the least costly, but requires tooling for print plates and sometimes cutting dies. The good news is, tooling is a one time cost and will be reused for your future runs of the same size and print scheme!
Flexographic printed boxes also require ink drawdown approval on the first run. Ink drawdowns are samples of custom ink builds created by packaging manufacturers to match target PMS colors.
Flexo inks are water based and have a degree of transparency. The substrate (paper color of your box) shows through the inks and can change how we see the selected color. That’s why approving the formulated color in real life is so important.
Flexographic (Flexo) Print Plate for Boxes
WHAT IS FLEXO PRINTING?
This design maximizes impact for Flexo, Folder, Gluer (FFG) friendly print.
Flexo printing is a high speed printing process that uses a soft print plate to transfer your design onto the substrate. Each color of your design will require its own print plate, so you can save on tooling costs by creating a 1-color design like the one seen here from Smartass and Sass. While you still achieve high impact printing with Flexo, if you have an intricate design, or low start up budget, Flexo may not be your best option - try Digital Printing instead.
The Good Stuff
Cost savings at middle to high quantities
Simple, bold designs look great
You can match 100% of Pantone colors with custom color builds
The Downside
Printing complexity is lower
Higher start up costs from tooling
Every color requires its own print plate
Subject to minimum order quantities (MOQ)
May not accommodate small text or fine details
Flexographic Print Examples

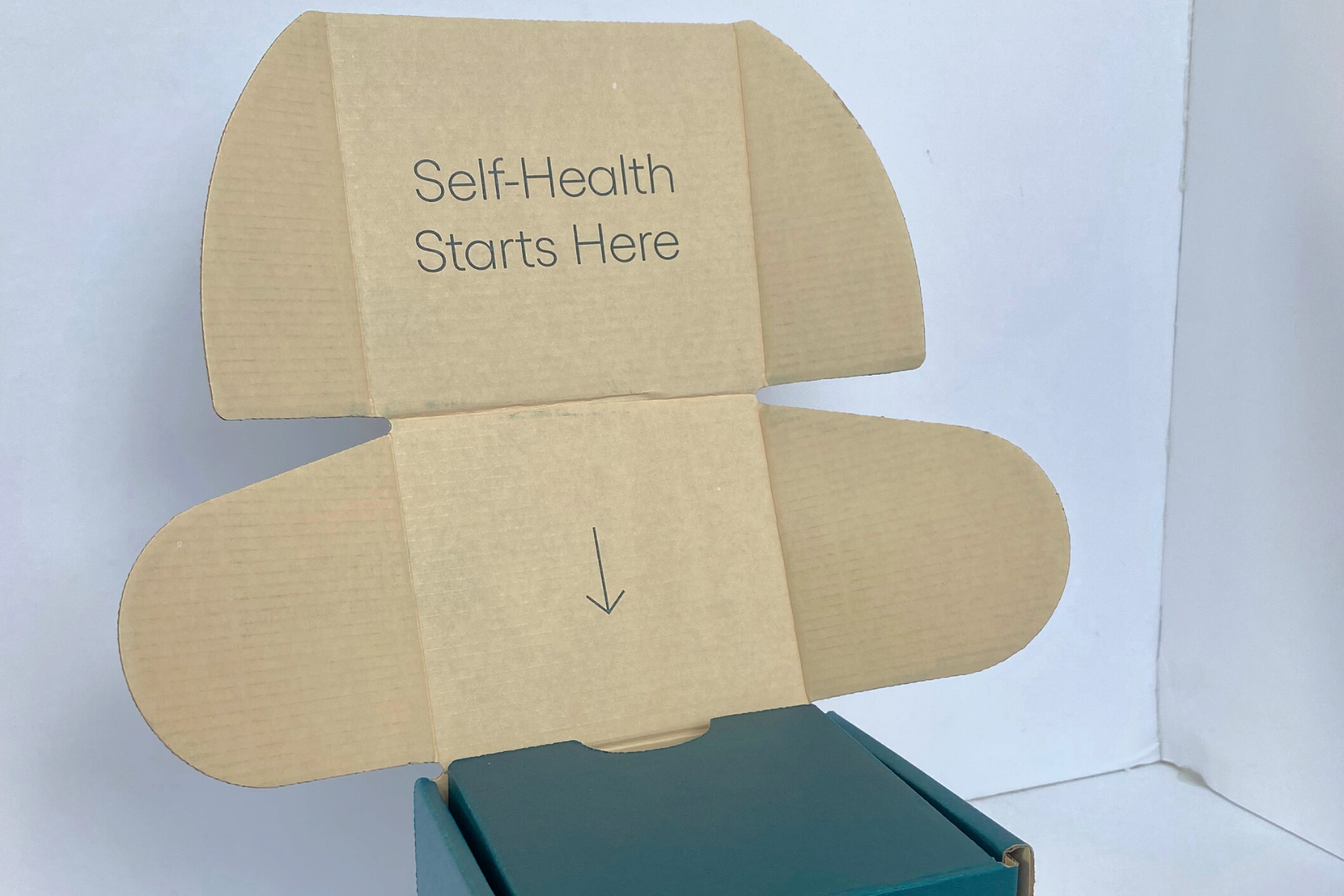
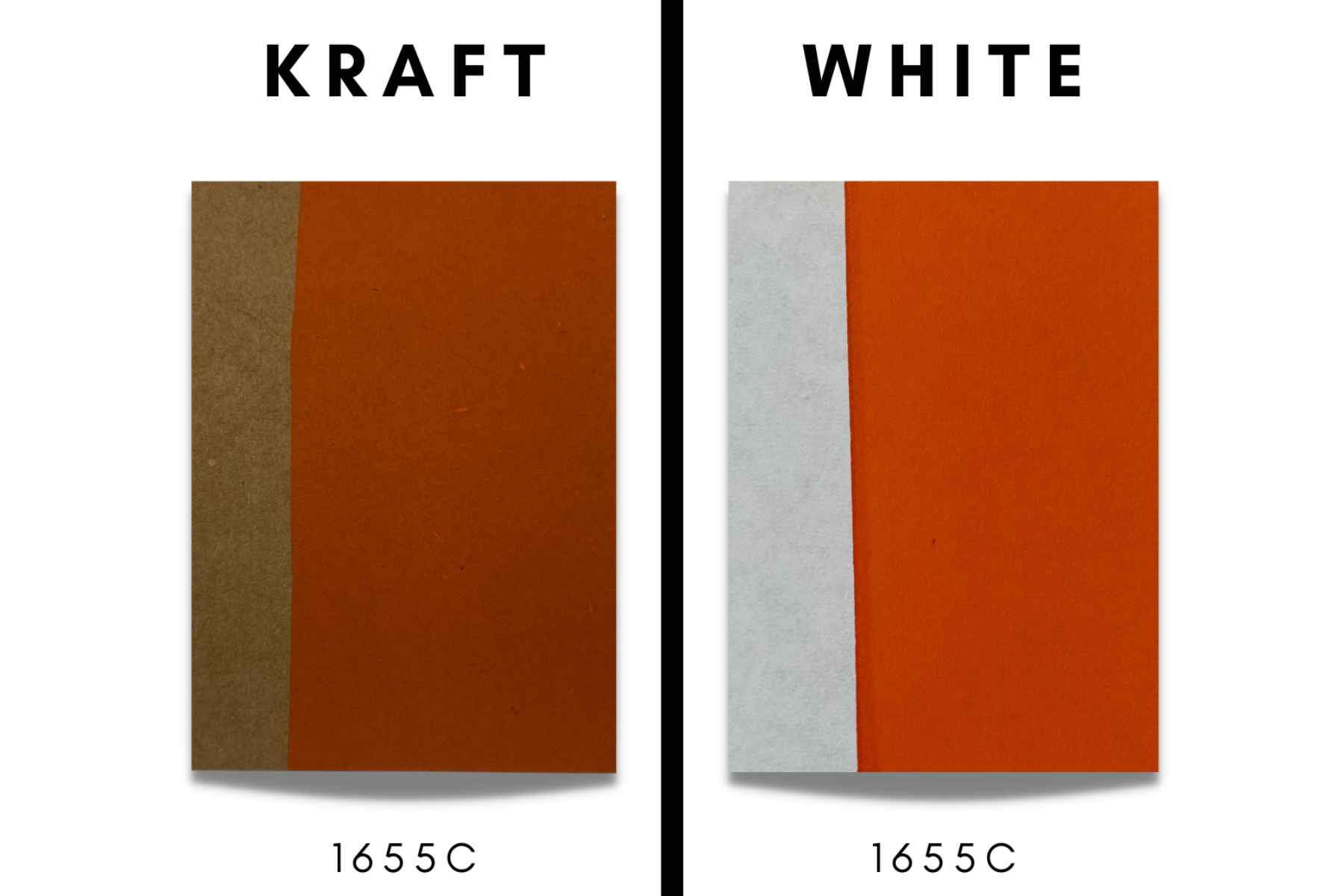
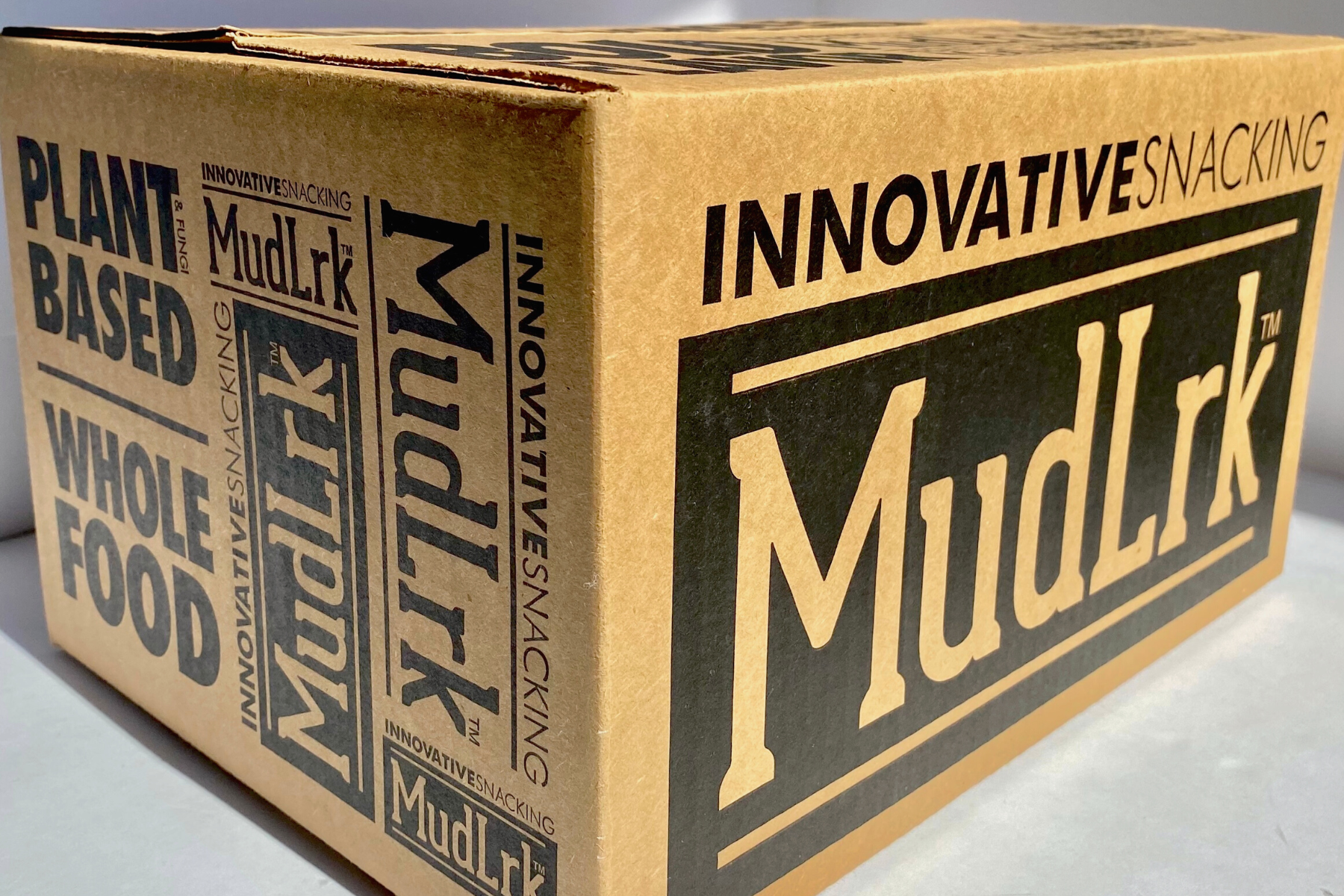
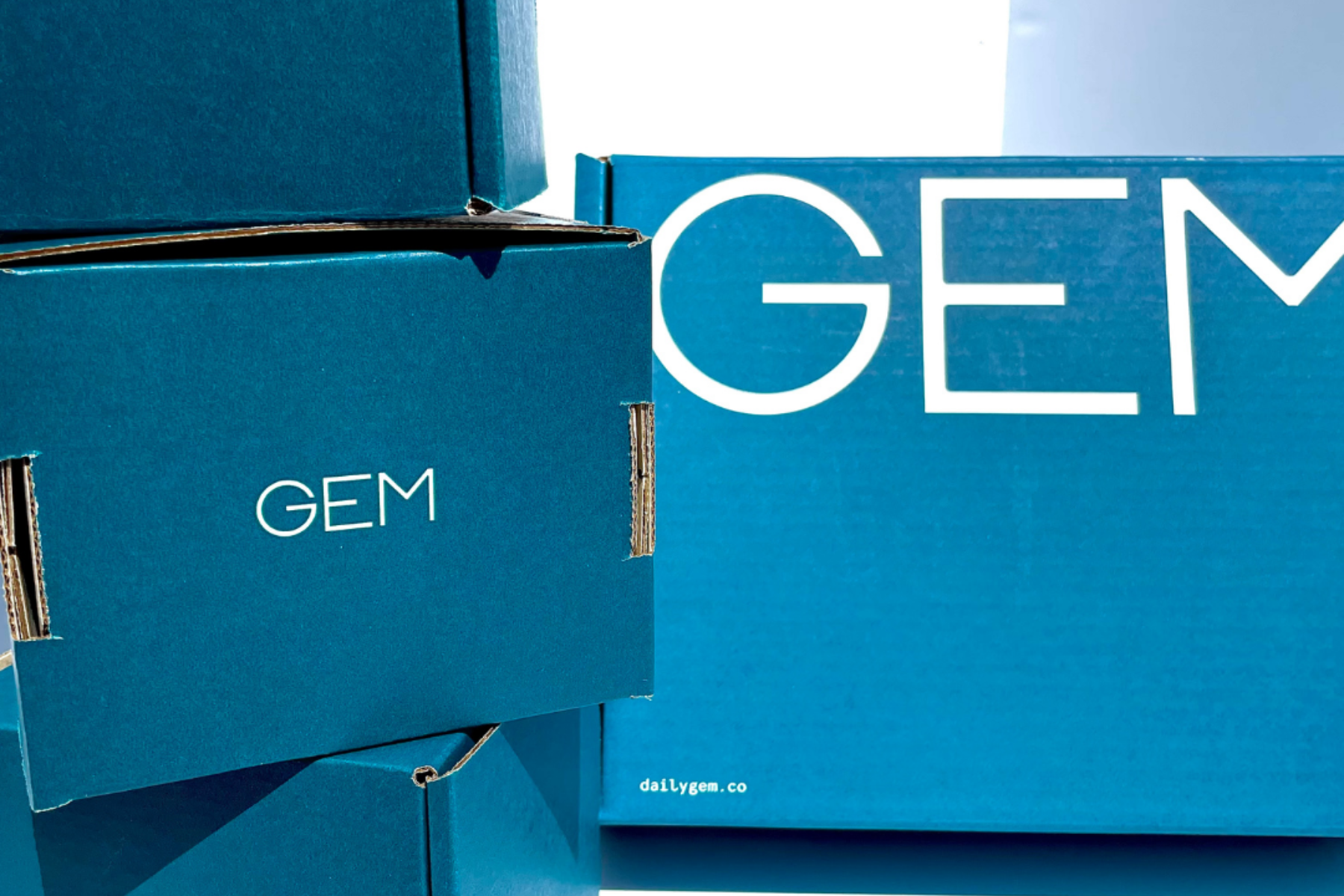
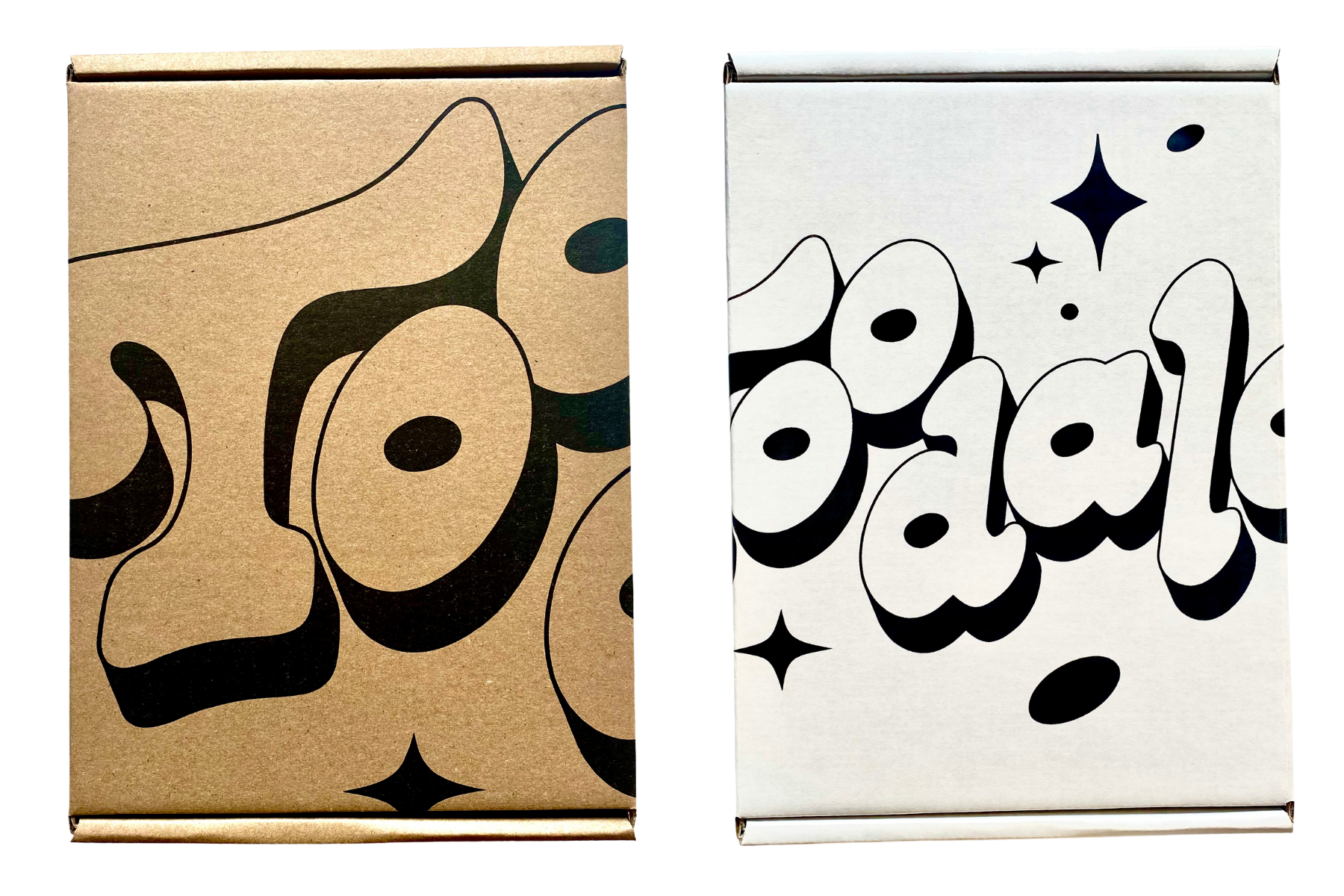
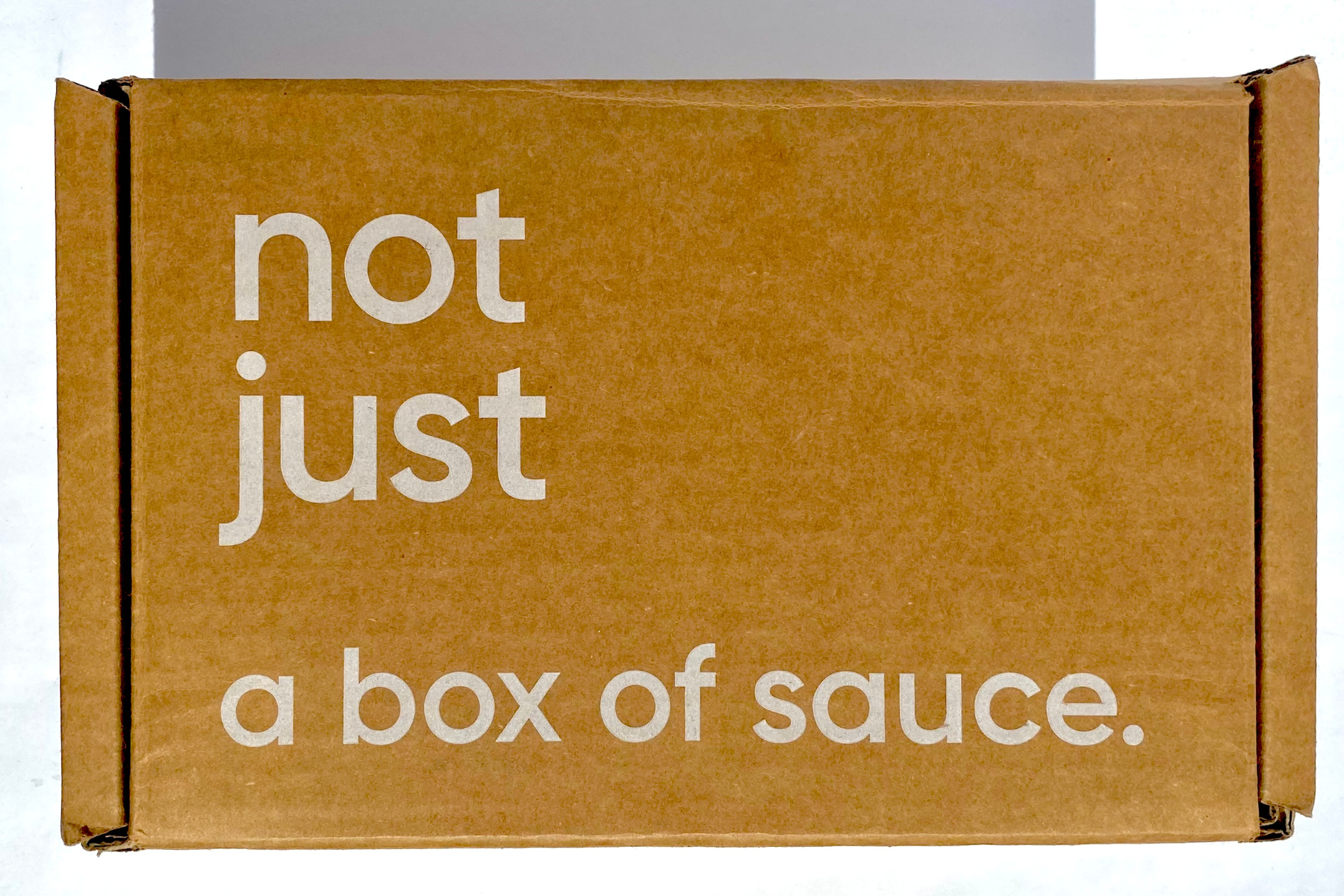
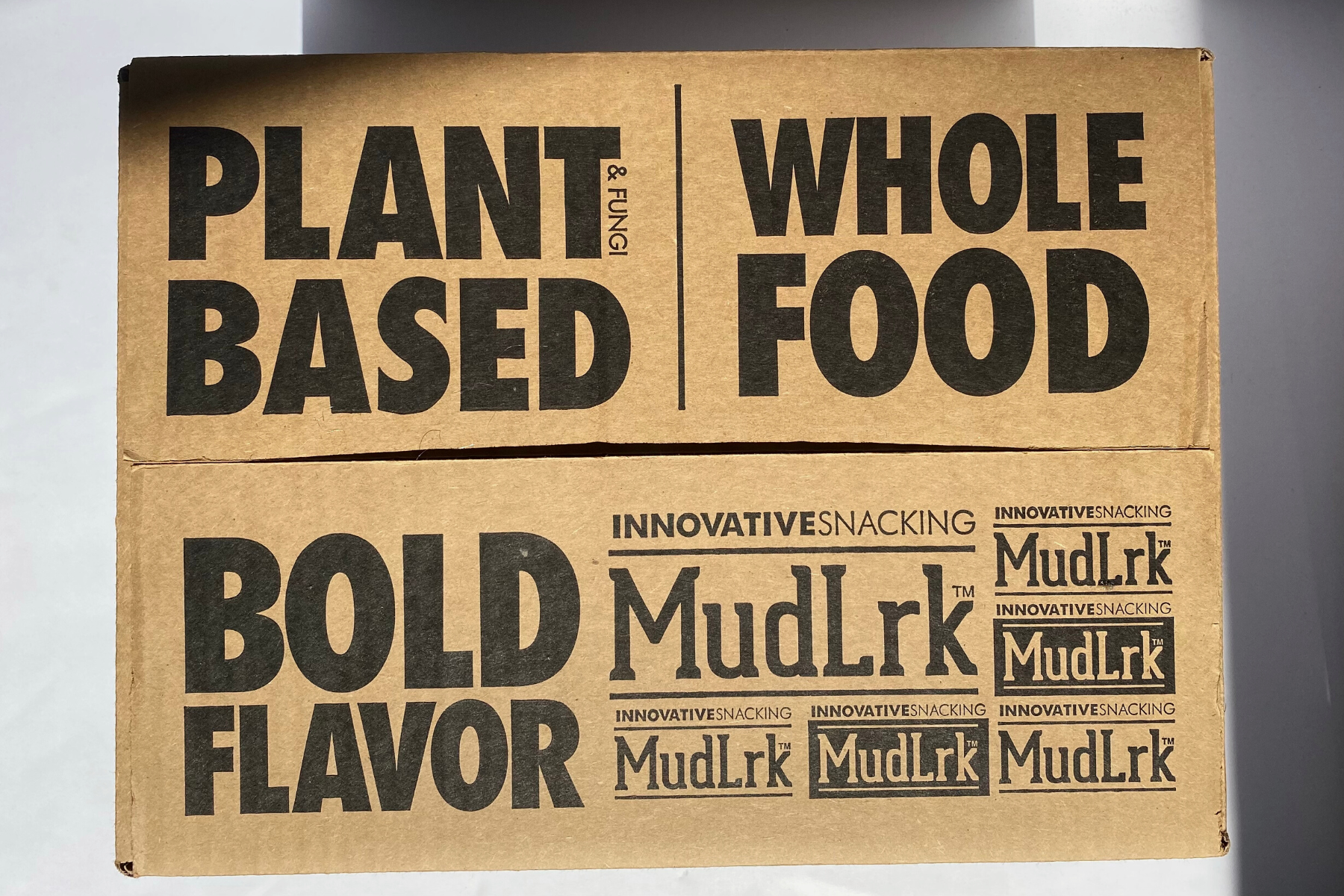
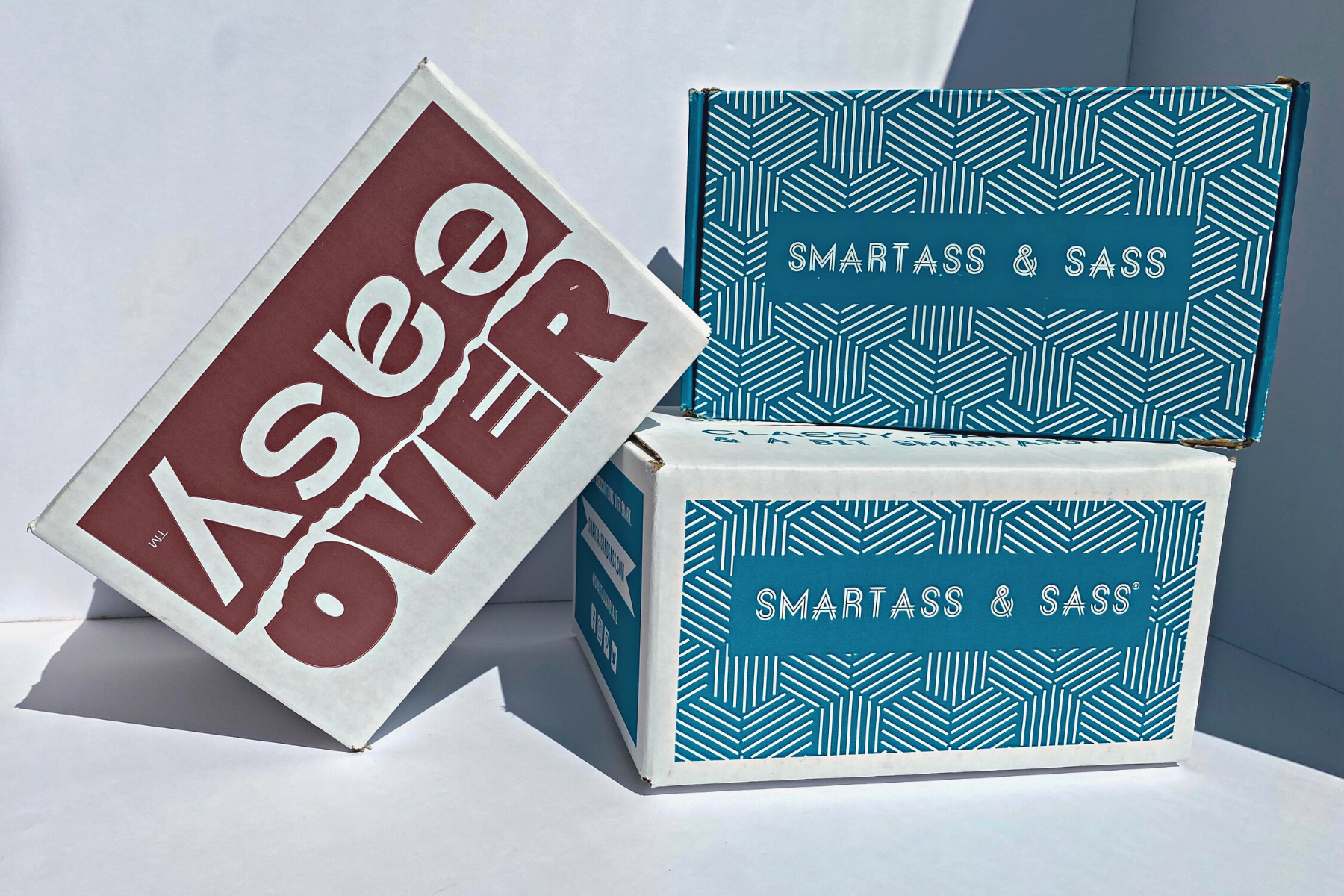
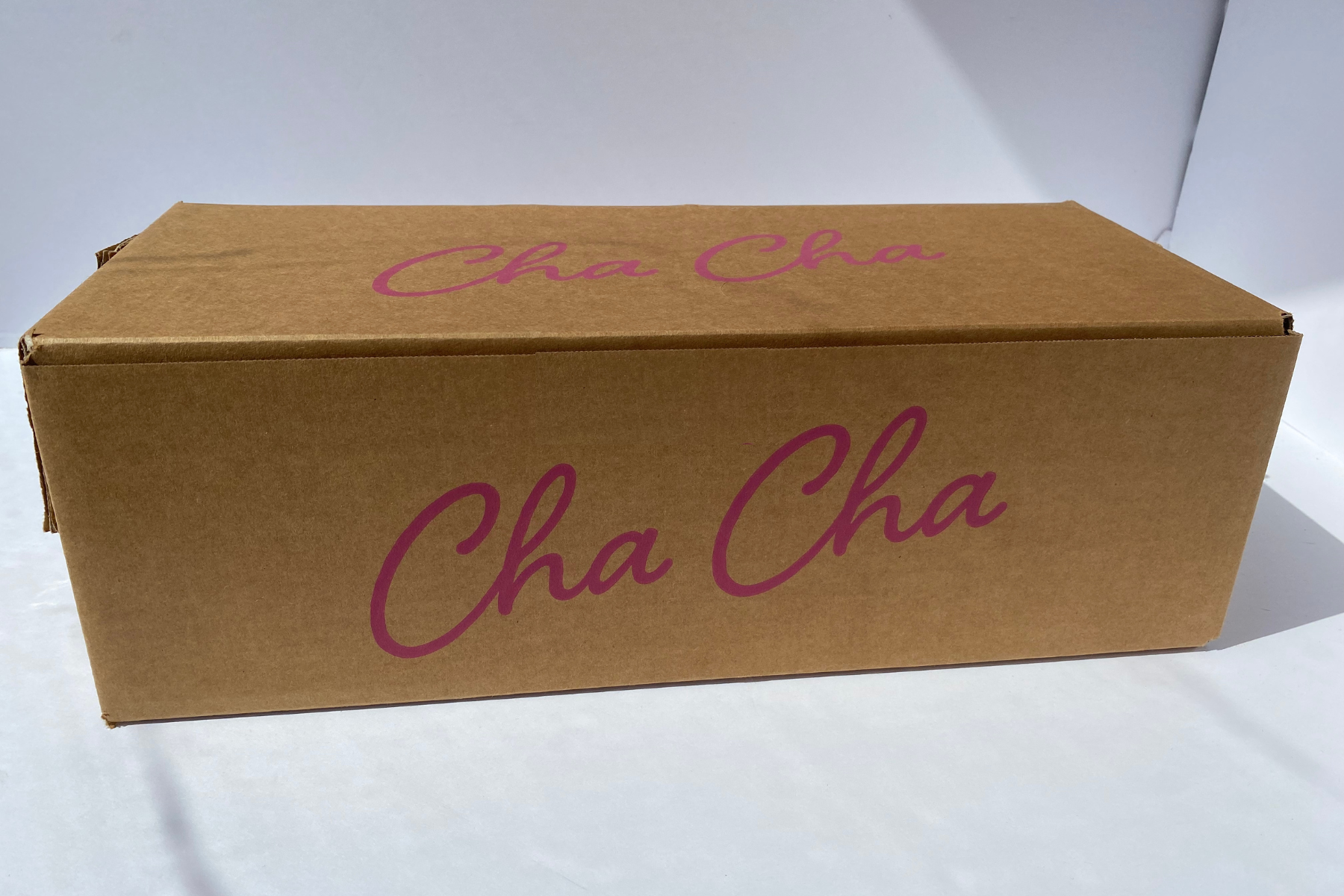
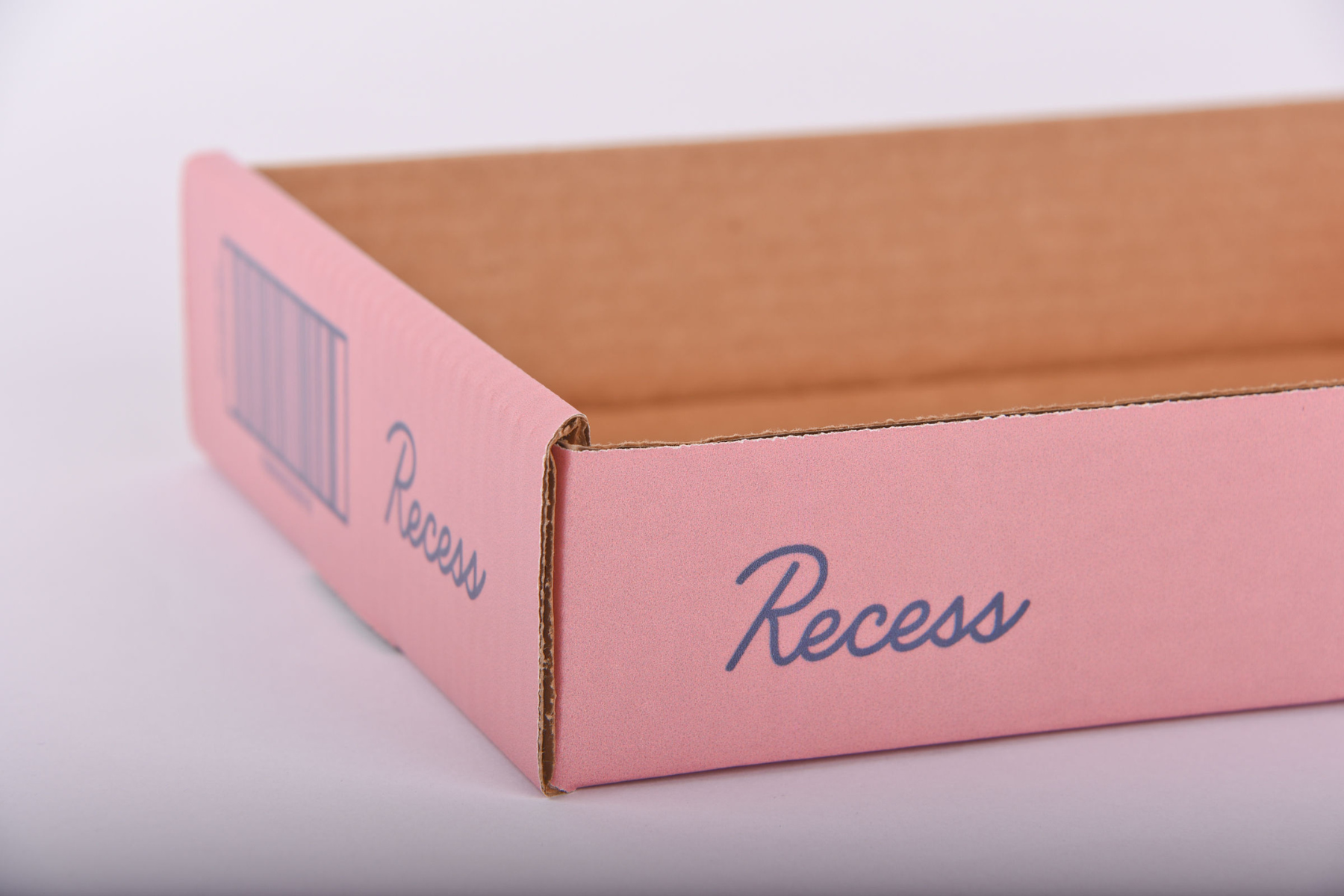